QRQC : 4 lettres qui ont changé ma manière de manager

LETTRE D’INFORMATION
N°41 – Juin 2025
Dernièrement j’ai été à nouveau confronté à 4 lettres magiques brandies par des qualiticiens et des managers : le QRQC
Il est vrai que dans ma carrière professionnelle ces 4 lettres ont marqué un changement radical dans ma vision du management des organisations. Comme beaucoup de démarche issue du Lean, il y a eu différentes compréhensions et pratiques. Rien que sur la signification de ces 4 lettres on peut trouver :
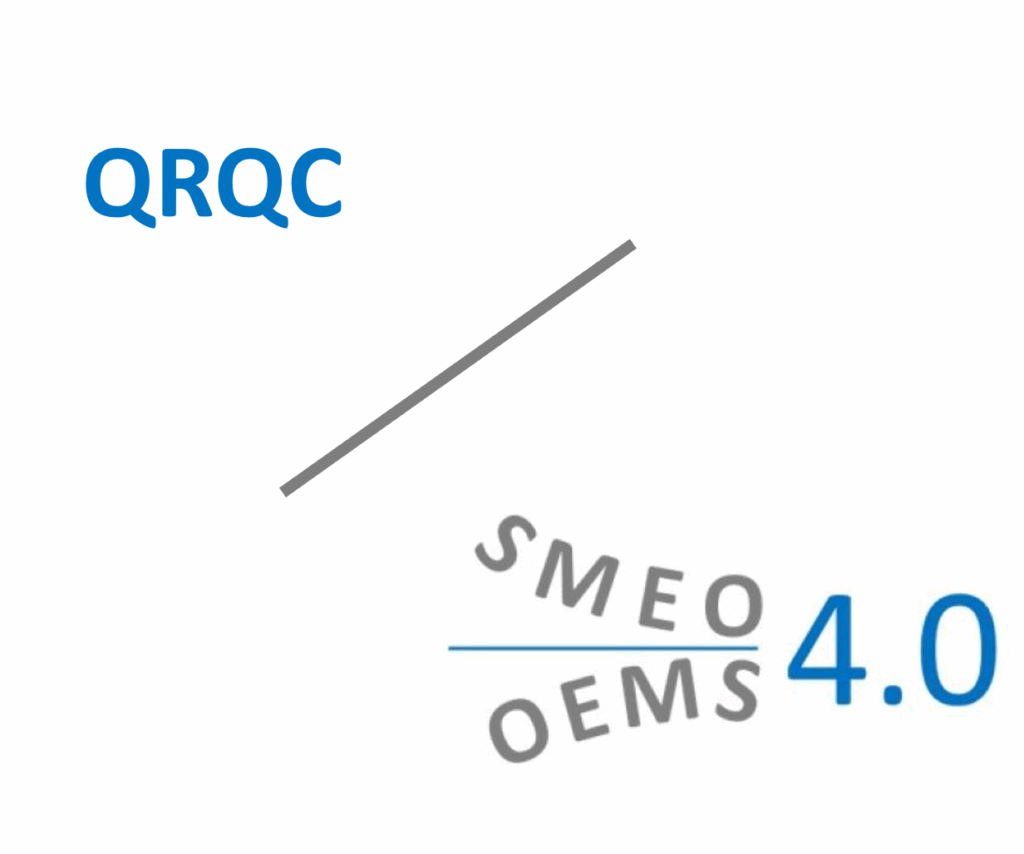
Identification des termes QRQC | Objectif |
Quick Response & Quality Control | management de la qualité sur le terrain |
Quick Response Quick Control | Contrôle qualité réactif |
Quick Response Quality Circle | Cercle de résolution de problème rapide |
Quick Response Quality Communication | Communication réactive sur les incidents |
Quick Response to Quality Concern | Prise en compte immédiate des anomalies |
Quick Recognition and Quick Correction | Détection et correction rapide |
Quick Reaction Quality Culture | Culture de réactivité face aux écarts qualité |
L’histoire du QRQC (Quick Response & Quality Control)
L’histoire du QRQC (Quick Response & Quality Control) s’inscrit dans le prolongement du développement des approches qualité terrain et des méthodes de résolution de problème issues du Toyota Production System.
Un peu d’historique vue de ma fenêtre :
🔹 Années 1950-1970 – Les fondements au Japon
- Naissance du Toyota Production System (TPS)
Sous l’impulsion de Taiichi Ohno, les principes de réactivité, d’autonomation (jidoka) et de résolution de problèmes à la source voient le jour.
➤ L’idée d’arrêter immédiatement la ligne en cas d’anomalie, via l’Andon, marque la volonté de ne pas laisser passer le défaut au poste suivant. - Emergence du Kaizen
Le travail d’amélioration continue, en petits groupes (cercles qualité), crée le socle culturel qui inspirera plus tard les QRQC.
🔹 Années 1980 – Diffusion du Lean et premières adaptations occidentales
- Introduction du Lean en Occident
Après la crise pétrolière, les constructeurs occidentaux s’intéressent aux performances industrielles japonaises.
➤ Des méthodes comme le 5S, le Juste-à-Temps et le Kanban commencent à être étudiées, notamment dans les usines automobiles européennes (plan Mercure chez Citroën). - Premiers cercles de qualité occidentalisés
Renault, PSA et d’autres entreprises introduisent des démarches inspirées des cercles qualité nippons, mais peinent à transposer la rigueur du terrain.
🔹 Années 1990 – Création du QRQC chez Nissan / Renault
- Contexte : Dans les années 90, Nissan puis Renault cherchent à renforcer leur capacité de réaction immédiate aux problèmes qualité détectés sur ligne.
- Mise au point du QRQC
➤ Le QRQC est formalisé comme un rituel de gestion de la qualité au poste de travail, visant à :- Réagir en temps réel à toute anomalie
- Résoudre rapidement les problèmes simples
- Escalader les problèmes complexes aux bons niveaux hiérarchiques
- Capitaliser et standardiser les solutions
➤ Ce système s’inspire fortement de :
- L’Andon
- Le 5 Pourquoi
- La culture du Gemba (terrain)
- Le management visuel
C’est en fin des années 90 que j’ai découvert à Nogent le Rotrou les premiers pas de l’adaptation par Valéo de cette pratique
Dans cette usine, fer de lance de la mise en pratique des démarches découvertes lors des visites réalisées dans le cadre du IMV program (voir « The Machine that change the world – J Womack, D.T.Jones & D Roos) nous avions un problème : des plans d’action dans tous les sens suite à de la résolution de problème réalisée par une multitude de collaborateur, mais peut de réalisation.
A l’époque, en tant que Responsable Etudes Série, nous avions avec mon équipe, plus de 900 « demande de modification » en cours de traitement et un taux de clôture qui ne dépassait pas les 10 par mois
Un Japonais a débarqué un matin (il me semble qu’il a été un temps Directeur Qualité Valeo) et mis le Comité de Direction face à son incapacité à animer toute cette valeur ajoutée
En allant dans l’usine, il a croisé un Opérateur à qui il a demandé quel était le point qui l’irritait le plus dans son activité et il a conduit le CoDir à aller au bout de la résolution de ce problème – C’est là qu’ils ont débarqué aux Etudes Série (cause racine : la conception d’un pignon sans poka-yoke) afin d’étudier, prototyper, valider avec l’opérateur, modifier le moule et mettre en production les composants modifiés afin d’éradiquer cet irritant
En sa présence, tout allait plus vite car toute action était immédiatement escaladée au bon Manager qui s’empressait de la réaliser (Cela n’était pas vraiment négociable)
Bilan : moins d’une semaine pour basculer en série, accord client compris
Cette expérience nous a montré que nous pouvions avoir des équipes rompues à la résolution de problème, cela n’était pas suffisant, nous devions en tant que Manager :
- Clarifier l’autonomie des équipes dans la réalisation des actions (Moyen, Autorité, Compétence)
- Escalader rapidement les actions au bon niveau de décision et de réalisation
- Formaliser au plus près du problème les éléments permettant de comprendre la situation pour pouvoir les transmettre sans déformation aux équipes pertinentes (QQOQCCP, Est/N’est pas, 4M, standard,5P,…)
- Faire un feedback très rapide aux équipes sur les décisions / actions menées
🔹 Années 2000 – Diffusion dans le Groupe Renault-Nissan et chez leurs sous-traitants
- Déploiement dans toutes les usines du groupe, avec des niveaux QRQC (N1 à N4) selon la complexité du problème.
- Adoption par les fournisseurs de rang 1, notamment dans les plastiques, l’emboutissage, l’assemblage électronique, etc.
- Mise en place de rituels QRQC : rituels courts quotidiens, animation au tableau,
- Mise en place de support facilitant la collecte des données initiales et produites par les équipes (8D version Lean, Tableau simplifié pour l’animation de QRQC,…)
Quoi de neuf depuis les années 2000 ?
Petit à petit des QRQC ont été mis en place dans différentes organisations industrielles et de Services
Globalement, mon expérience dans le déploiement et l’accompagnement de cette démarche me permet d’identifier 2 catégories de pratique :
- Un QRQC de niveau 1 (équipe) permettant d’impliquer les collaborateurs mais qui est très lourd à pérenniser et dont les résultats, obtenus avec beaucoup d’énergie, découragent petit à petit les chefs d’équipe. Souvent intégré dans les AIC (Animation intervalle Court) mais sans escalade et QRQC aux niveaux supérieurs
- Une démarche QRQC portée par l’ensemble des Managers, colonne vertébrale de l’animation des équipes et véritable culture de l’entreprise.
Inutile de vous dire qu’en terme d’efficience et qualité de vie au travail, il n’y a pas de comparaison
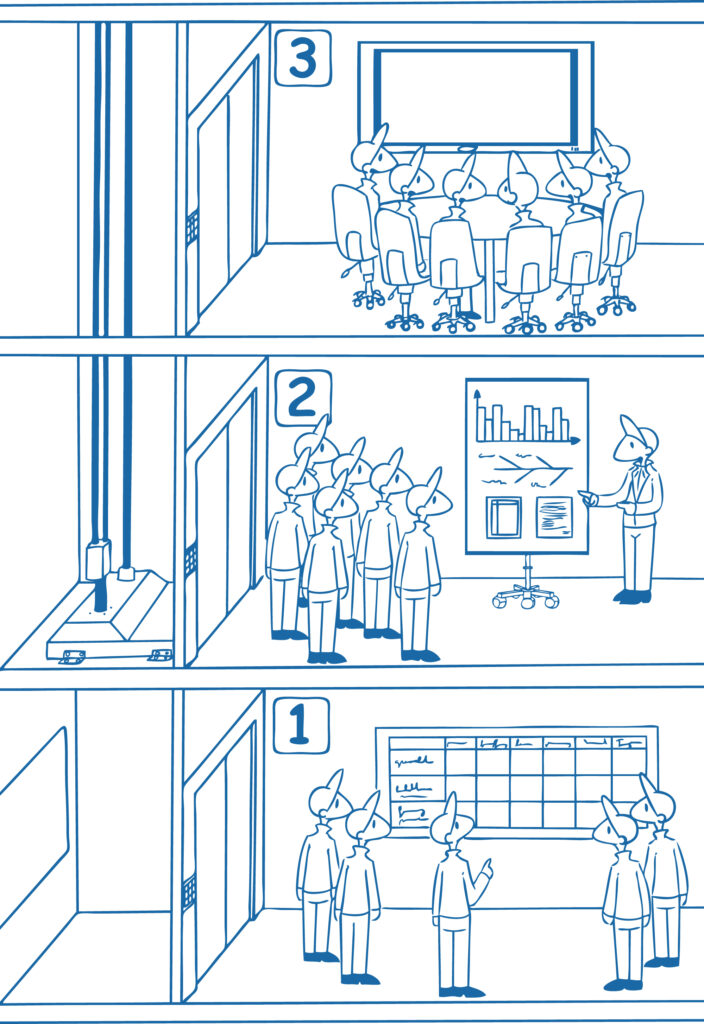
Le QRQC comme pilier de l’excellence opérationnelle
- Devenu un rituel clé du Système de Management de l’Excellence Opérationnelle, le QRQC est aujourd’hui :
- Un outil de pilotage quotidien des unités de production et des fonctions Support
- Un système d’escalade structuré, dynamique, piloté par le top management
- Une culture d’appropriation de la qualité par les opérateurs et les fonctions « Support »
- Un outil de formation continue, par le questionnement et la résolution
Il implique des compétences de savoir-faire au niveau des Managers. Il peut aujourd’hui être supporté par des applicatifs numériques évitant les ressaisies et pertes d’information, les lenteurs de transmission tout en facilitant les routines de management.
Mais les outils, même numérique ne remplace pas les savoir-faire des managers en termes de :
- Capacité à identifier si un événement est bien un problème
- Dissocier la non-application d’un standard de l’absence ou l’amélioration nécessaire d’un standard
- La maitrise de son autonomie et celle de son équipe, dans leurs Moyen, Autorité et Compétences (MAC)
- Focaliser son équipe sur un nombre restreint d’actions d’amélioration réalisables et réalisées rapidement
- D’identifier « Qui fait quoi » dans l’entreprise : accès immédiat et ergonomique aux processus
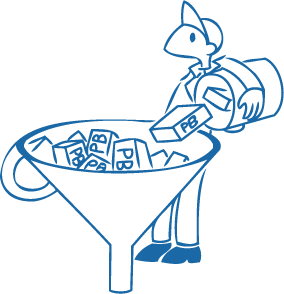
Dans le Système de Management de l’Excellence Opérationnelle, que je mets en place chez mes clients, des avancées significatives rendues possibles grâce à l’apport du numérique, permettent :
- D’améliorer la gestion des plans d’actions individuels ou collectifs
- De faire évoluer en continu les Processus et/ou les documents de savoir-faire
- D’atteindre et transmettre plus facilement les éléments aux personnes pertinentes
- De garantir qu’avant de réinventer la roue, les équipes s’appuient d’abord sur les bonnes pratiques et référentiels de l’entreprise
Vous souhaitez vous faire accompagner dans la mise en place de la démarche QRQC ou souhaitez avoir un diagnostic de vos pratiques, n’hésitez pas à me contacter contact@dded.fr
Vous souhaitez faire évoluer votre SMQ vers un Système de Management de l’Excellence Opérationnelle (SMEO 4.0), n’hésitez pas à me contacter contact@dded.fr